Aqualisa's warranty covers all parts and labour providing the fault is with the product and not relating to issues such as accidental damage or installation. Warranties will range dependent on your product - warranty information can be found at the bottom of the product registration page please click here to view this. Please note: In order to claim under the Aqualisa Warranty, you will need to have registered your guarantee and provide a valid proof of purchase. We are unable to arrange any service call bookings or send free parts until this has been completed.
Frequently Asked Questions
Explore the list of frequently asked questions below, where you can find answers and videos to support you with shower installation, key features and usage to improve your shower experience.
General Information
Aqualisa can be contacted by phone, email, or live chat, Please click here for our contact details. Live chat can be accessed on any page where you see the pink chat box in the bottom right corner of your screen.
The majority of Aqualisa showers do not have a name or model on them but understanding the type of shower will help narrow the search. Please search for your shower from the list below;
Digital Main Control Identification
Bi-Metallic / Aquavalve Products
Wax Capsule Products
If you start water flow by turning a knob, this will be one of our Thermostatic range.
If you start water flow by pushing a button but the shower has no flashing lights, this will be an electric model. Electric showers should have a badge indicating a name and KW rating but if this is missing, it may be obtainable from a plastic coated sticker on the underside of the casing. KW ratings can be found on the shower's engine but this would require isolation the property's main fuse board before removing the shower casing.
If you start water flow by pushing a button and the shower has flashing lights, this will be one of our Digital / Smart range.
If you cannot find your shower or need further assistance, please e-mail our customer service team at [email protected] and attach some photographs of the product for us to identify.
Product technical drawings are available to download directly from product pages. You can search our website for the product you are looking for either by the product name or code. Alternatively, you can browse our complete list of installation guides here.
You can register your shower by clicking here. Please note: In order to claim under the Aqualisa Warranty, you will need to have registered your guarantee and provide a valid proof of purchase. We are unable to arrange any service call bookings or send free parts until this has been completed.
The guarantee period on a processor when purchased with a complete shower is 5yrs. If the processor unit is purchased on its own as a spare part then this will come with a 2yr guarantee. For a full list of Aqualisa's warranty periods, please click here.
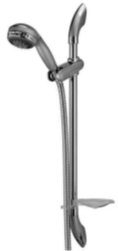
1. Remove the cover from the bottom rail bracket.
2. Remove the single screw holding the bracket to the wall and remove the bracket from the bottom of the rail. (The rail may also separate from the top bracket once removed)
3. Slide the old handset holder off the rail (dependent on the type of handset holder, you will need to use the pinch mechanism, button, or twist lever to release the grip on the rail)
4. Pass the rail through the replacement handset holder whilst keeping the gripping mechanism released from the rail. Replace the soap dish / gel hanger if fitted.
5. Ensuring the handset holder is the correct way up, re fit the rail into the rail end bodies taking care to engage the location slot onto the lugs. Ensure the white rail end clip is fitted into position into the bottom rail end body and secure the rail bracket and replace the screw, ensuring the rail and rail end bodies remain firmly engaged.
6. Re fit the cover.
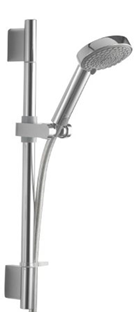
1. Remove the cover from the bottom rail bracket by pulling downwards, releasing it from the clips on the grey bracket inside.
2. Remove the single screw holding the grey bracket to the wall and remove the bracket from the bottom of the rail (The rail may also separate from the top bracket once removed).
3. Slide the old handset holder off the rail (dependent on the type of handset holder, you will need to use the pinch mechanism, button, or twist lever to release the grip on the rail).
4. Pass the rail through the replacement handset holder whilst keeping the gripping mechanism released from the rail. Replace the soap dish / gel hanger if fitted.
5. Ensuring the handset holder is the correct way up, re fit the rail into the rail end bodies taking care to engage the location slot onto the lugs and replace the screw on the bottom bracket, ensuring the rail and rail end bodies remain firmly engaged.
6. Re fit the cover.
Note: To remove this rail, you will require the removal tool provided. This can be ordered under part 910020 if required.

1. On the back of the bottom chrome rail bracket, insert the removal as picture and lever the locking tab towards to wall.
2. Gripping the rail between the brackets, slide the rail upwards to expose the single fixing screw.
3. Remove the single screw holding the chrome bracket to the wall and remove the bracket from the bottom of the rail.
4. Slide the old handset holder off the rail (dependent on the type of handset holder, you will need to use the pinch mechanism, button, or twist lever to release the grip on the rail).
5. Pass the rail through the replacement handset holder whilst keeping the gripping mechanism released from the rail. Replace the soap dish / gel hanger if fitted.
6. Ensuring the handset holder is the correct way up, re fit the rail through the top bracket. Reposition the bottom bracket and return the screw to fix the bracket to the wall.
7. Side the rail back into the bottom bracket, ensuring the hole at the bottom of the rail lines up with the bracket’s locking tab so it clicks into place.
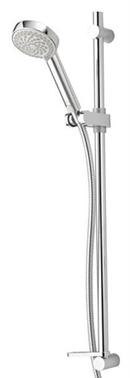
1. Remove the cap from the bottom rail bracket to expose the fixing screw. This screw secures both the rail and bottom bracket in place.
2. Remove the screw to release the rail and bracket. Slide the rail downwards and out of the top bracket.
3. Slide the old handset holder off the rail (dependent on the type of handset holder, you will need to use the pinch mechanism, button, or twist lever to release the grip on the rail).
4. Pass the rail through the replacement handset holder whilst keeping the gripping mechanism released from the rail. Replace the soap dish / gel hanger if fitted.
5. Ensuring the handset holder is the correct way up, re fit the rail through the top bracket. Reposition the bottom bracket and return the screw to fix the rail and bracket to the wall.
6. Replace the cap to the bottom rail bracket.
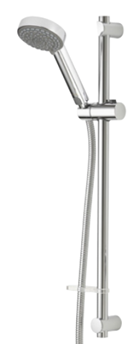
1. Remove the chrome cap from the top rail bracket to expose the fixing screw. This screw secures both the rail and bottom bracket in place.
2. Remove the screw to release the rail and bracket. Slide the rail downwards and out of the top bracket.
3. Slide the old handset holder off the rail (dependent on the type of handset holder, you will need to use the pinch mechanism, button, or twist lever to release the grip on the rail).
4. Pass the rail through the replacement handset holder whilst keeping the gripping mechanism released from the rail. Replace the soap dish / gel hanger if fitted.
5. Ensuring the handset holder is the correct way up, re fit the rail through the top bracket. Reposition the bottom bracket and return the screw to fix the rail and bracket to the wall.
6. Replace the chrome cap to the top rail bracket.
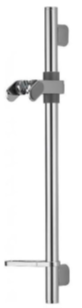
1. Using a 4mm allen key, remove the fixing bolts from the top and bottom ends of the rail to release it from the brackets.
2. Slide the old handset holder off the rail (dependent on the type of handset holder, you will need to use the pinch mechanism, button, or twist lever to release the grip on the rail).
3. Pass the rail through the replacement handset holder whilst keeping the gripping mechanism released from the rail. Replace the soap dish / gel hanger if fitted.
4. Ensuring the handset holder is the correct way up, re fit the rail on to the brackets. Before pushing it home, insert the fixing bolt into the rail end cap and secure it to the top bracket using a 4mm Allen key. Repeat for the bottom bracket.
General Installation/Maintenance (all products)
Aqualisa showers are designed to work on the following high pressure water systems:
Please note: our Thermostatic and Digital products are not designed to work on mixed supplies (e.g. mains cold / gravity hot) or combination cylinders due to inadequate cold water capacity and working head distance.
Digital products:
If the Smart Valve currently fitted is pumped (A2) this will need to be replaced.
If the Smart Valve currently fitted is standard HP (A1), this would suggest that the gravity water system has a separate booster pump to pressurise the water. In this case, the Smart Valve is already compatible for the change to high pressure, however the settings on the logic will need to be switched "HP Combi" if intended to be fitted on a combi boiler water system.
Thermostatic products - Bimetallic products changing to combi boiler system:
Products with the grey universal cartridge fitted will require a flow regulator to be inserted into the elbow of the cold water supply going into the shower. The regulator slows the cold flow down, helping to balance the amounts of hot and cold water mixing together. If the regulator is not fitted, this may result in poor showering temperature. On concealed models, if the elbow is difficult to access inside the wall, a pink multipoint cartridge (part # 022802) can be purchased. Pink cartridges are specifically designed for combi boiler systems and does not require the cold flow regulator.
Products with an orange gravity cartridge will require a pink multipoint cartridge (part # 022802) to be fitted.
Thermostatic products - Siren, Aspire, AQSL, & AQDL models changing to combi boiler system:
The appropriate hot water flow regulator will need to be fitted in the hot inlet of the valve. 3 regulators are available dependent on the KW rating of the boiler.
Thermostatic products - Bar Valves & DCVs:
No changes will be required.
Electric showers:
These products should already be fitted to a dedicated cold mains water supply which will be separate from the gravity system - if this is the case, no changes will be required.
Ceiling and wall mounted Fixed heads Aqualisa fixed shower heads have a basic threaded connection and simply unscrew from the fixed arm. Looking up at the spray plate, turn the head anti-clockwise to remove it. Please Note: Most of our fixed heads include a ball-joint which allows a small degree of angling. Occasionally the connection of the ball joint to the head unscrews, instead of where the ball-joint screws to the arm. If this occurs, it will need to be removed from the arm (by also turning anti-clockwise) and re-attached to the head if required. If the head is being removed for replacement, the new head will be supplied with a ball-joint.
Adjustable Heads
Most of our adjustable heads simply unscrew from the hose but our range also includes models with an "anti-twist" feature to prevent kinking and damage to the hose.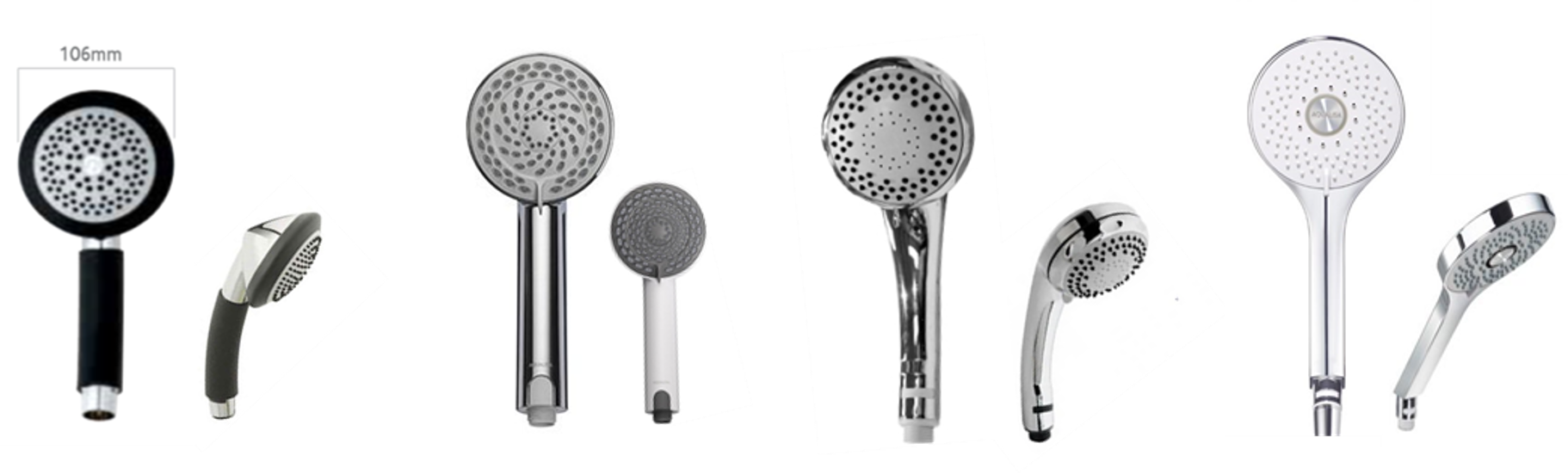
Axis head-kit
With the spray plate facing away from you, at the base of the handle, you will see a horseshoe shaped clip. Remove the clip from the base of the handle by gently pulling each end out and sliding the clip free from its seating. Once the clip has been removed, this should allow the handset to be pulled away from the hose, leaving the adapter still in place which can now be unscrewed from the end of the hose.Harmony head-kit
With the spray plate facing you, you will see a button at the base of the handle. Push and hold the button in to lock the ant-twist in place and the hose can now be simply unscrewed. The button should be pressed until the hose has been fully removed, or re-attached to ensure a tight seal has been achieved.Opto head-kit
If you look at the base of the handle on the shower head (just above where the hose connects), you will see a thin rectangular slot on the front and back of the handle which should be dark grey in colour. If you press down on the slot on the back of the handset - the hose connector will be released and should slide free from the handset, you can then unscrew the fitting from the end of the hose.Vita head-kit
With the spray plate facing you, you will see a grey rectangular insert at the base of the handle. Pushing the insert in will pop it out on the back side of the handset; this should now allow the handset to be pulled away from the hose, leaving the adapter still in place which can now be unscrewed from the end of the hose.Aqualisa products are very low maintenance and there is very little for you to do to keep them in good working order. We advise that you use warm soapy water or non-abrasive bathroom cleaning products / chemicals as these can damage the chrome plating and cause it tarnish. Micro Fiber cloths are also effective at keeping the shower clean and polished. If you live in a hard water area, which is prone to scale and calcification, you may need to descale the shower head every few months (or as and when needed). Scale can be cleaned by soaking the head in warm water and white vinegar (2:1 ratio) for approx. 20 minutes. Our shower heads also feature rub clean jets - gently rotating the jets with your fingers to help break up any scale inside the jets. To avoid rapid scale build up, we advise that after use you tilt the shower head at an angle, which will allow any excess water to drain away.
Smart Valves:
Inlet centres have remained the same across all generations of our Smart valves. A2 and A1 Smart Valves share the same centres however, the location of the mixed supply pipe differs and would need altering if changing from gravity to high pressure.
Digital / Smart Exposed models:
The following exposed models are interchangeable as the bottom rail bracket fixing point is in the same location (the top bracket can be situated where required so does not affect compatibility). This advice refers to full product replacement and not a simple change of control due the differences in some controller mounting plates.
The following Exposed models utilise the main control's backplate as a bracket and feature variety of fixing points. Replacing with a different model will require new holes to be drilled and may leave old holes on display...
Concealed Digital Smart models:
Due to the differences in main control mounting plates, new fixing holes would be required and may leave old holes on display. Some wall repair may be needed to ensure the new fixing holes can be drilled. Dependent on the new model, the data cable would need to be exchanged for different type. On concealed models, data cables should have been installed in a suitable conduit or trunking to allow for easy removal and replacement. Please see below for details on rail kits, wall outlets and fixed arms.
Bar valves with a single adjustable head:
All bar valves have 150mm pipe centres and can be fitted on the existing male threads coming from the wall.
Bar valves with both adjustable and fixed heads or fixed head only:
All bar valves have 150mm pipe centres and can be fitted on the existing male threads coming from the wall. If the model has changed however, a new hole will likely be required for the wall stay that supports fixed head rail. Please note: If you are changing from a single adjustable head and wish to now include a fixed head, this will not be compatible with exposed pipework.
Aquavalve - concealed models (pre 2004, excluding brass bodies):
Apart from the Classic, all inlet centres will be the same however, the outlet will need to be reduced from 22mm to 15mm. In order to access the valve body, a hole between 130mm - 150mm would be required behind the wall plate. If the model being replaced is the Classic, the inlets will need to be reduced from 164mm to 150mm and the outlet reduced from 22mm to 15mm.
Aquavalve - concealed models (post 2004, excluding brass bodies):
Valve bodies have remained the same from 2004 so no alterations will be required. In order to access the valve body, a hole between 130mm - 150mm would be required behind the wall plate.
Aquavalve - brass body models:
Brass body models have remained the same since launch... Concealed models have threaded connections and therefore, have no fixing centres. Exposed models have inlet centres of 194mm.
Aquarian models or models based on aquarian (exposed torpedo shaped showers):
All models have 150mm centres but new fixing holes will be required for the cartridge backplate if replacing an E96. Due to the location of the new fixing holes being so close to the original, wall surface repairs will be required to ensure a solid fixing of the backplate.
Aquastream (MK1 / MK2 to MK3):
Providing the supply pipes are rear fed, all models have 65mm inlet centres. If surface pipework is required, the centres will need adjusting to 65mm for both top or bottom entry. The foot print on the MK3 also differs from the MK1 / MK2 so an extra inch of clearance will be required to ensure this fits and new fixing holes will need drilling. Please note: The wall will need to be fully tiled beneath the existing shower for the installation to be completed.
Electric Showers:
Unless like for like, electric showers are not considered direct replacements. Recommendations for an alternative is based on cold water inlet connection type / location, electrical wiring location and current KW rating. Shower footprints differ along with fixing points so new holes will likely be required or may leave old fixing points on visible. The wall will need to be fully tiled beneath the existing shower for the installation to be completed.
Adjustable rail kits:
Like for like shower models aren't guaranteed to include the same rail as before. Many of our new products feature a retro-fit rail kit, designed to fit over the existing screw holes on the majority of installations. In some cases however, a longer rail may need to be purchased in order for the existing fixing holes to be utilised with the new floating rail bracket.
Concealed wall outlets:
Due to connection type, pipe size, and fixing points, alterations may be required to install a wall outlet supplied with a new product.
Fixed wall / ceiling arms:
Due to connection type and fixing points, alterations may be required to install a fixed arm supplied with a new product.
For a detailed answer, please visit the 'HOW DO I REMOVE MY ADJUSTABLE SHOWER RAIL' FAQ.
Flow & Leak Questions
You will need to establish firstly whether the dripping is constant or if it stops over time. The easiest way to do this is to remove the head and hose from the shower or in the case of fixed heads, remove the head from the arm.
IF THE DRIP CONTINUES
This indicates a potential fault with your shower - please call our customer service team on 01959 560010 and select the appropriate option whether in or out of warranty. For further information on warranty periods, these can be found at the bottom of the product registration page - please click here to view this.
Please note: In order to claim under the Aqualisa Warranty, you will need to have registered your guarantee and provide a valid proof of purchase. We are unable to arrange any service call bookings or send free parts until this has been completed. If you have previously done this, you will not need to do this again.
IF THE DRIP STOPS
This is likely due to water retention and is not a product fault. Shower heads will continue to drip until the water level falls below the jets on the head. Restrictions can slow this process slower - we would advise to check for kinks or twists in the hose or lime scale blockages in the spray plate of the shower head. A kinked hose can be unravelled by removing it from the outlet and letting it naturally untwist. Limescale can be cleaned by soaking the head in warm water and white vinegar (2:1 ratio) for approx. 20 minutes. Our shower heads also feature rub clean jets - gently rotating the jets with your fingers to help break up any scale inside the jets.If your shower struggles to produce water (especially hot water) and spits or splutters in use, the most common cause is an air lock. Air locks occur on gravity water systems, normally within the pipe-work of the hot supply. Airlocks can develop over time or occur all of a sudden. You may find that the air lock only affects the shower and all your other appliances are fine - this would be because the shower has its own dedicated water supplies and the restriction has developed within this pipe-work.
Please follow the steps below to clear the air from the pipe work:
You may need to repeat this process a few times to clear the air entirely but afterwards the hot and cold flow should be the same.
Whatever the root cause may be, airlocks are never caused by a product fault. If you find you have recurring air locks you may need to consult a plumber, or if the air will not clear and the flow continues to splutter then you may be experiencing cavitation, draw down or possibly an air leak...
WHAT IS CAVITATION?
Cavitation refers to air bubbles which are being released into the pipe-work. This is normally caused by the hot water temperature being set too high - we advise that it is set to no higher than 65ºC.WHAT IS DRAW-DOWN?
Draw down occurs when there are restrictions in the shower's hot and cold supplies, such as a build up of scale. When the shower is in use, these restrictions can cause air to be sucked air down the open vent pipe. The open vent pipe is the pipe which rises from the top of the hot water cylinder and hangs over the cold water tank. There is a simple method of testing for draw-down, you simply run the shower and then hold a glass of water up to the end of the open vent pipe. If the water is sucked down the pipe then draw-down is occurring. Draw down is not a product fault - please contact a plumber for assistance.WHAT IS AN AIR LEAK?
An air leak refers to a leak somewhere on the supply to the shower. Whilst the shower is in use, air is sucked in through this gap. If you think you are experiencing this, please contact your plumber.Flow spluttering is commonly due to an air lock, especially if your shower is fitted on a gravity water system.
Flow rates are influenced by several factors. These include:
The model of shower installed.
The water system in the property.
Pipework installation - size and type of pipework, number of 90 degree bends.
Other outlets being used at the same time as the shower.
Debris in the supply pipes or filters.
Please note: due to these factors, any maximum flow rates quoted are approximate only and are based on an optimal shower installation.
Reducing flow - Digital / Smart products:
Black, orange & watermelon (pink) Smart Valves feature an "Eco" setting which reduces flow by approximately 33% and can be selected following the steps below. Please note: "Eco" is not compatible with combi boiler systems as this will likely cause temperature fluctuation.
Switching to "Eco":
1. You would first need to locate the fused spur where the Smart Valve connected power supply is connected. This is likely sited close to the Smart Valve. If you are not familiar with the Smart Valve or its location, this is the box that mixes the water and controls shower temperature. Smart Valves are often installed in a loft space, airing cupboard or under the bath. In any case, it will be within 10m of your showers main control as this is the maximum length of the data cable connecting to the main control. Once located, the fused spur will need to be turned off - depending on the installation this may be a switch box, plug socket or small box where the fuse can be popped out.2. Isolate the power to the Smart Valve using the fused spur.
3. Remove the lid(s) on the Smart Valve by loosening the single screw:
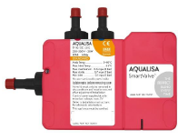
On standard HP units (1 lid only), this is located next to the outlet pipe.
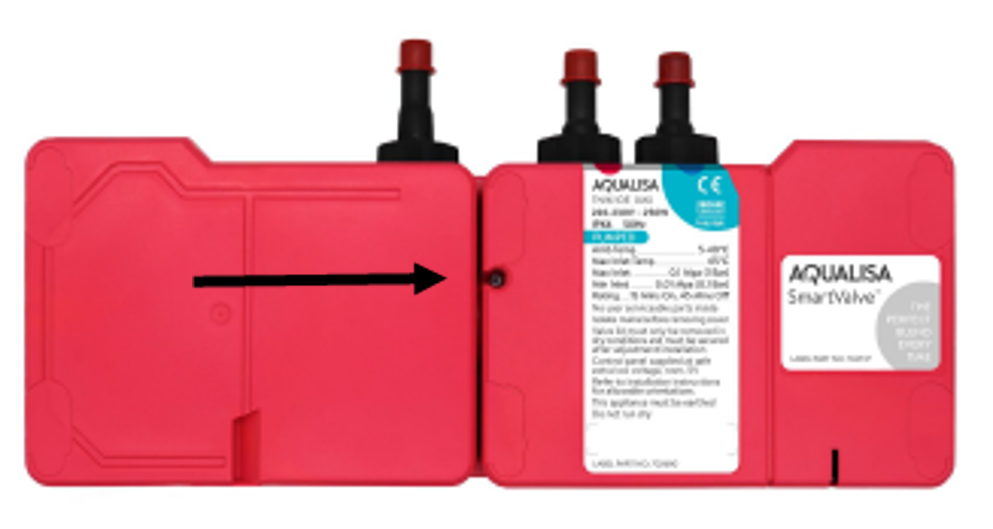
On pumped units (2 lids), the screw is located between both lids.
On the box labelled Logic Module, insert a flat head screw driver into the slot on the blue dial under "MODE" (bottom left corner of logic module). Please ensure you select the correct "Eco" mode that is compatible with your water system i.e. HP or Gravity.
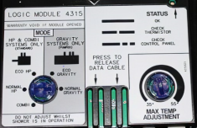
Once changed to the correct "Eco" setting, replace the lid(s) and turn the fused spur back on.
Reducing flow - Harmony heads:
Many of our products include the Harmony head which features an "Eco" spray setting which can reduce flow up to 25%. This can be set by turning the lever on the spray plate to face the 3 o'clock position. Please note: The "Eco" setting may cause combi boiler systems to experience temperature fluctuations. Harmony heads are available for our showers ranges including a specific model for Electric showers and can be purchased separately if required.Flow too powerful (pressure):
Pressure (the force, rather than volume of water) is governed by the Bar pressure of your water system. This includes the output Bar pressure of a booster pump / integrally pumped shower in gravity installations. Reducing flow via an "Eco" will not lower pressure. Dependent on the installation, a pressure reducing valve (PRV) may be compatible - please see below...Gravity systems with booster pumps / integrally pumped showers:
We do not recommend the use of PRVs on our pumped products as this could damage the pump.Combi boiler, ground / air sourced heat pump systems:
A PRV may be an option but you would need to consult a plumber.Unvented systems:
PRVs should feature as part of the installation and generally operate at 2-3 Bar of pressure. If you are experiencing an increase of pressure on an unvented installation, this could indicate that the air gap inside the tank needs servicing. This would need to be assessed by a plumber qualified to work on unvented tanks.This is not recommended as it can reduce flow and empty the hot and cold tanks too quickly. On Gravity water systems, the minimum cold tank capacity is 225L (50 gallons) per shower. We do not stipulate a hot tank capacity as this is dictated by the size and demand of the household.
This could be caused by a blockage within the shower head or hose. We would advise to check for any restrictions such as kinks or twists in the hose or lime scale blockages in the spray plate of the shower head, this can be cleaned by soaking the component in warm water and white vinegar (2:1 ratio) for approx. 20 minutes. If you are on a gravity fed water system with a cold water tank, we would advise to check for an air lock. Refer to "how do I clear an airlock?" for further information.
Smart / Digital Products
You would first need to locate the fused spur where the Smart Valve connected power supply is connected. This is likely sited close to the Smart Valve. If you are not familiar with the Smart Valve or its location, this is the box that mixes the water and controls shower temperature. Smart Valves are often installed in a loft space, airing cupboard or under the bath.
In any case, it will be within 10m of your showers main control as this is the maximum length of the data cable connecting to the main control. Once located, the fused spur will need to be turned off - depending on the installation this may be a switch box, plug socket or small box where the fuse can be popped out.
Once turned off, please wait approximately 3 minutes and turn the power back on - after a short period you should hear a noise from the Smart Valve which will be the valves resetting.
For information about Aqualisa Smart App please click here
Please see the instructions below for each digital/smart shower
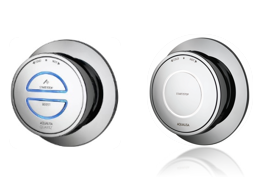
1. On the underside of the control, you will see a single self-retaining screw with a cross-head – loosen the screw to release the control.
2. Carefully slide the control upwards and away from the mounting plate to expose the data cable.
3. The cable can now be pulled out of the back of the control. If replacing the control, the cable must be firmly pushed into the control to ensure a good connection and seal.
1. On the underside of the control mounting box, you will see 2 self-retaining screws with cross-heads – remove the screws to release the control.
2. The top of the control has lugs that lock into the mounting box - carefully slide the control downwards and away from the mounting box to expose the data cable.
3. The cable can now be pulled out of the back of the control. If replacing the control, the cable must be firmly pushed into the control to ensure a good connection and seal.
1. On the underside of the control, you will see a single self-retaining screw with a cross-head – loosen the screw to release the control.
2. Using the Q Lever, carefully rotate the control upwards anti-clockwise to release the control from the mounting plate lugs and expose the data cable*.
3. The cable can now be pulled out of the back of the control. If replacing the control, the cable must be firmly pushed into the control to ensure a good connection and seal.
*If the model is a Q Smart or edition, the data cable will not be visible as this is fitted directly into the mounting plate. In this case, the control will have 4 gold pins that contact with the mounting plate to form a connection.
1. On the underside of the control, you will see a single self-retaining screw with a cross-head – loosen the screw to release the control.
2. Carefully slide the control away from the mounting plate to expose the data cable.
3. The cable can now be pulled out of the back of the control. If replacing the control, the cable must be firmly pushed into the control to ensure a good connection and seal.
1. Dependent on the installation type, the control releases in 1 of 2 ways: Exposed control (rail through ceiling) / pre 2007 concealed models - Push the control upwards, and the retaining ring will move to release the control from its lower securing lugs. Concealed control - On the underside of the control, you will see a single self-retaining screw with a cross-head – loosen the screw to release the securing end cap.
2. Carefully pull the control away from the mounting plate to expose the data cable.
3. The cable can now be pulled out of the back of the control. If replacing the control, the cable must be firmly pushed into the control to ensure a good connection and seal.
1. With this model, the internal PCB is replaced rather than the full control.
2. Carefully pull the control knobs off. Carefully remove the wall plate which will be secured using silicone sealant. This will expose the PCB which connect to the control knobs.
3. Remove the PCB from its housing.
4. The cable can now be pulled out of the back of the control. If replacing the control, the cable must be firmly pushed into the control to ensure a good connection and seal.
1. Dependent on the orientation of the control the screw is in 1 of 2 places: Shower control (vertical orientation) On the underside of the control you will see a single self-retaining screw with a cross-head – to release the control. Bath control (horizontal orientation) On the right of the control you will see a single self-retaining screw with a cross-head – to release the control.
2. On the opposite end to the screw, the control has a lug that locks into the back plate- carefully slide the control away from the mounting plate to expose the data cable.
3. The cable can now be pulled out of the back of the control. If replacing the control, the cable must be firmly pushed into the control to ensure a good connection and seal.
1. Dependent on the orientation of the control the release clips is in 1 of 2 places: Shower control (vertical orientation) On the underside of the control you will see the clip – press in to release the control. Bath control (horizontal orientation) On the right of the control you will see the clip – press in to release the control.
2. On the opposite end to the clip, the control has a lug that locks into the back plate- carefully slide the control downwards and away from the mounting box to expose the data cable.
3. The cable can now be pulled out of the back of the control. If replacing the control, the cable must be firmly pushed into the control to ensure a good connection and seal.
Yes - the seals inside pumped Smart Valves are designed to only withstand a maximum of 1Bar of pressure vs the standard units which go up to 7Bar. It is a common misconception that the logic module inside the Smart Valve can be simply switched over to HP - this will only turn the pump off and does nothing for the seals inside the unit. Connecting a pumped Smart Valve to a high pressure water system will invalidate the warranty and could cause leaking which will not be covered.
You will need to isolate the power and water to the shower, disconnect the data cable at the processor unit / Quartz™ smart valve and then disconnect the black push fit 90° elbow located directly above the shower, fitted to the shower’s down pipe. Remove the fixings that hold the shower to the wall and carefully lower the shower down from the ceiling. Pull the 10m data cable through into the bathroom. Once the cable is in the room with you, you can slide the old holder off the top of the rail and over the data cable, and reverse to fit the new holder. As this is a technical job we usually recommend an Aqualisa service engineer carries out this work.
A2 and A1 Smart Valves share the same hot and cold inlet centres however, the location of the mixed supply pipe differs and would need altering if changing from gravity to high pressure. In many cases, this will be an extra elbow connection - below are images both Smart Valves and the location of the mixed supply pipe.
A2 Gravity Pumped Smart Valve
A1 Gravity Pumped Smart Valve
1. You would first need to Unscrew the 4 feet each corner of the Smart Valve.
2. Isolate the main circuit on which the Smart Valve is connected
3. Remove the data cable from the Smart Valve. To do this, the lid must be removed by loosening the single screw between the 2 lids of the Smart Valve (image below). The data cable can be removed by pushing on the lever that secures the cable plug into the Logic Module.
4. Water must also be isolated. Smart products are supplied with isolation valves which should have been used in the installation. Using a flat head screwdriver, turn the groove 90 degrees so that it is positioned across the valve rather than parallel with the pipe. Repeat for the remaining 2 isolation valves. If the isolation valves are also required to be replaced, further isolation of the water system will be required on the hot and cold tanks to avoid draining down the system. If the system must be drained, this could potentially cause airlocks when refilled.
5. Remove the Smart Valve from the pipes. To do this, push on the release collars (black rings) on the isolation valves to disengage the grippers from the black processor spigots.
The main controls vary cosmetically and flow rates are higher for the Quartz Range. Please note: flow rates are approximate only and based on installation factors.
On single outlet models, Quartz range has a boost feature where Visage does not. Please note: The boost feature is not designed to operate on Combi boiler systems.
On Divert models, Quartz has a dedicated button to select each outlet where Visage has a single button that needs to be held down to switch outlets. Quartz Divert also features a wider range of outlet options compared to Visage.
Thermostatic Products (including Aquastream)
New installations or following any internal servicing
Check that the on/off control knob is not fitted upside down - this will cause the inside of the knob to be in contact with the pump's micro switches when the flow is turned off. To position this correctly, the flow graphic sticker on the edge of the knob should sit at approximately 5 o'clock with the fin positioned vertically when the shower is turned off.
All installations:
If not due to the above, the issue will be related to the micro switches which may need to be replaced... Check that the loom assembly is fitted correctly over the cartridge as this could cause the micro switches to stick. Check for signs of damage to the micro switches or any signs of water having been in contact with them. The presence of water would suggest a leak from the unit which would need to be investigated further to identify the source of the leak. Check for the switches getting stuck down (the micro switches should click when pressed)
Bi-metallic Cartridges: (similar to that pictured)

If the leak is coming from the shower head in the form a constant drip, this is likely due to the hot o'ring being incorrectly positioned, damaged or not renewed. These models have had 2 different designs of valve body during their production as well as solid brass bodies. The hot o'ring is installed differently with each design...
2 piece valve bodies (1979 - 2004) Also includes Aquastream MK2:
Identified by a large square fixing plate which fixes to the wall, the hot o'ring must be placed in the back of the body inside the groove. To remove the old o'ring, this is best hooked out using something like a dental pick - older o'rings may have hardened and could break up so it is important to ensure it has been fully removed before replacing it with the new one.1 piece valve bodies (2004 - current) Also includes Aquastream MK3:
Identified by 4 corner fixing points which fix to the wall, the hot o'ring must be fitted on the end of the tube running inside the metal coil. Before fitting the o'ring, the white circlip should be fitted first inside the groove on the end of the tube as this supports the o'ring to ensure it seals when the cartridge is pushed into the valve body.Solid brass bodies (Aquatique and Aquavalve 700 models):
The hot o'ring must be placed in the back of the body inside the groove. To remove the old o'ring, this is best hooked out using something like a dental pick - older o'rings may have hardened and could break up so it is important to ensure it has been fully removed before replacing it with the new one. Due to machining tolerances, an oversized hot o'ring may sometimes be required although the majority of time, the one provided is sufficient.If the hot o'ring has been correctly positioned and the shower is still dripping, please check the o'ring for any signs of damage.
In the case that the o'ring is not the issue, it may be due to the valve body itself and requires changing. Sufficient access of 130-150mm will be required behind the wall plate to replace this.
Pumps (including booster pumps, Aquastream & pumped digital smart valves)
Initially, we would advise to check for an air lock within the pipe work to begin with as this can cause the pump to become noisy. A step by step guide to clear an air lock is available on "how do I clear an airlock?" FAQ above.
If this does not resolve the problem, this could indicate an issue with the product - please call our customer service team on 01959 560010 and select the appropriate option whether in or out of warranty. For further information on warranty periods, these can be found at the bottom of the product registration page - please click here to view this.
Please note: In order to claim under the Aqualisa Warranty, you will need to have registered your guarantee and provide a valid proof of purchase. We are unable to arrange any service call bookings or send free parts until this has been completed. If you have previously done this, you will not need to do this again.
General Information
Aqualisa's warranty covers all parts and labour providing the fault is with the product and not relating to issues such as accidental damage or installation. Warranties will range dependent on your product - warranty information can be found at the bottom of the product registration page please click here to view this. Please note: In order to claim under the Aqualisa Warranty, you will need to have registered your guarantee and provide a valid proof of purchase. We are unable to arrange any service call bookings or send free parts until this has been completed.
Aqualisa can be contacted by phone, email, or live chat, Please click here for our contact details. Live chat can be accessed on any page where you see the pink chat box in the bottom right corner of your screen.
The majority of Aqualisa showers do not have a name or model on them but understanding the type of shower will help narrow the search. Please search for your shower from the list below;
Digital Main Control Identification
Bi-Metallic / Aquavalve Products
Wax Capsule Products
If you start water flow by turning a knob, this will be one of our Thermostatic range.
If you start water flow by pushing a button but the shower has no flashing lights, this will be an electric model. Electric showers should have a badge indicating a name and KW rating but if this is missing, it may be obtainable from a plastic coated sticker on the underside of the casing. KW ratings can be found on the shower's engine but this would require isolation the property's main fuse board before removing the shower casing.
If you start water flow by pushing a button and the shower has flashing lights, this will be one of our Digital / Smart range.
If you cannot find your shower or need further assistance, please e-mail our customer service team at [email protected] and attach some photographs of the product for us to identify.
Product technical drawings are available to download directly from product pages. You can search our website for the product you are looking for either by the product name or code. Alternatively, you can browse our complete list of installation guides here.
You can register your shower by clicking here. Please note: In order to claim under the Aqualisa Warranty, you will need to have registered your guarantee and provide a valid proof of purchase. We are unable to arrange any service call bookings or send free parts until this has been completed.
The guarantee period on a processor when purchased with a complete shower is 5yrs. If the processor unit is purchased on its own as a spare part then this will come with a 2yr guarantee. For a full list of Aqualisa's warranty periods, please click here.
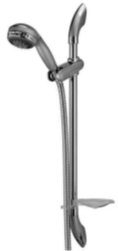
1. Remove the cover from the bottom rail bracket.
2. Remove the single screw holding the bracket to the wall and remove the bracket from the bottom of the rail. (The rail may also separate from the top bracket once removed)
3. Slide the old handset holder off the rail (dependent on the type of handset holder, you will need to use the pinch mechanism, button, or twi